Technologies
Nanovia has these technologies in its manufacturing facility
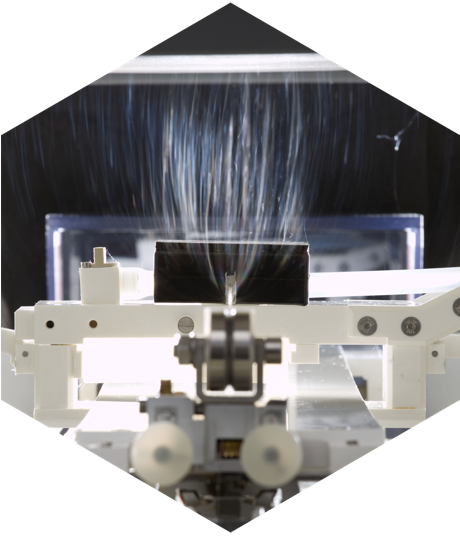
Producing nanofiber layers for a carrier
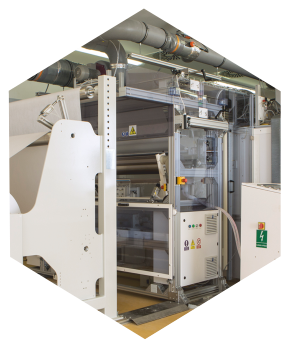
Securing adhesion of nanofibrous layer to a substrate
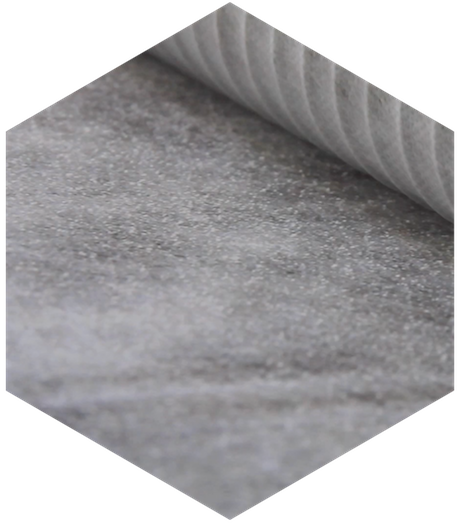
Connecting fabric materials with nanofiber layer by powder adhesive
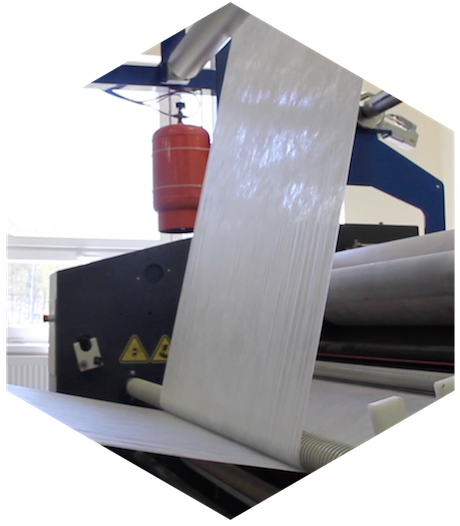
Providing one-sided or double-sided lamination of nanofiber layer with fabric materials
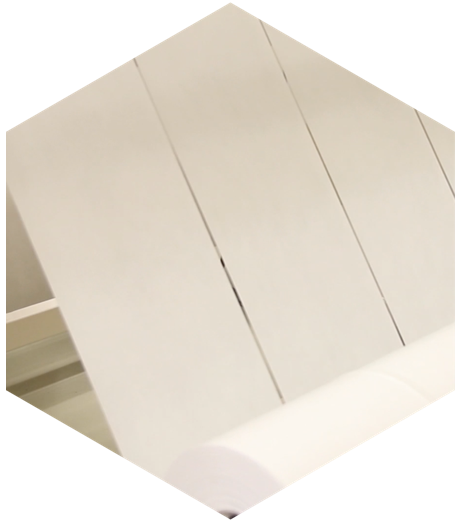
Slitting laminated fabrics into strips
The barrier fabric developed by Nanovia is inherently three-layer or multi-layer fabric laminates. Ordinary non-woven material of spunbond or meltblown type having a layer of submicron fibres (nanofibers) in between them is used as the outer layers.
Mechanical connection of the three-layer fabric laminates or two-layer filter media is addressed by means of applying the adhesive solution onto the substrate before being covered by nanofibers or bonding one or both sides by powder adhesive.
Using the lamination technologies allows extending the applications for nanofiber materials into various industries and final products.
A critical parameter of usability of e.g. filter media with a nanofiber layer is ensuring sufficient adhesion between the carrier medium and the nanofiber layer. The layer cohesiveness is significantly affected by a workability of media into finished products (filters).
Production technologies
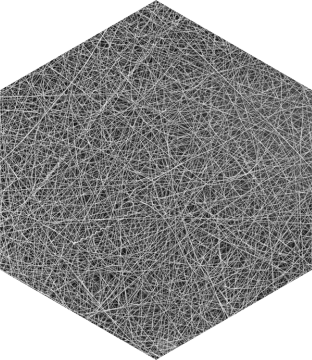
Nanofibres
Nanofibres are fibres the diameter of which is smaller than 900 nm, the typical fibre diameters ranges between 100–500 nm. Due to this fact, the nanofiber layers are distinguished by special properties:- large surface area
- high porosity
- small pore size
- possibility of nanofiber additivation, for example by biologically active substances
Production of nanofibers
Nanovia s.r.o. uses the Nanospider™ technology for the production of nanofibers, based on the principle of spinning the polymer solution in electrostatic field.
Nanovia has a laboratory machine intended for the development of new materials and preparation of samples. Industrial production of barrier fabrics, filter materials, nanofiber membranes and other nanofiber materials is provided by several industrial machines Nanospider™.
Production technology operating data:
- maximum operating width of 1650 mm, nanofiber layer maximum width of 1600 mm;
- maximum processable winding diameter of 1200 mm;
- tube diameter at inlet of 76 mm, at outlet of 76 or 152 mm.
Polymers PA6 and PVDF are predominantly used for the industrial production of nanofiber materials for barrier fabrics and filter materials by Nanovia, other polymers are also possible.
The production of nanofiber materials takes place in areas of cleanliness class 8 according to ISO 14664.
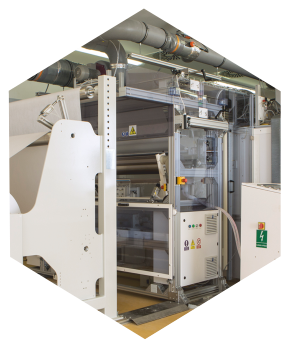
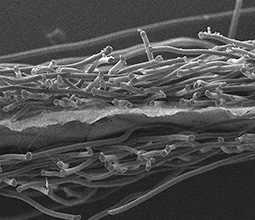
Fabric laminates
Barrier fabrics and filter media by Nanovia are the three-layer or multi-layer fabric laminates containing at least one nanofiber layer enclosed between the non-woven fabrics or textiles.
Nanofiber layer in Nanovia laminates is usually very thin (basis weight of between 0.05 to 1.0 g/m²), therefore it has no sufficient mechanical properties for its handling. If the nanolayer is fixed only on the carrier which makes is mechanically firmer and dimensionally stabilized, its handling is possible; however, its further processability is still very difficult because of possible mechanical abrasion during processing and using the final product. Only the reversible protection of nanofiber layer ensures its mechanical and shape stability (tensile strength, minimal elasticity) and resistance against abrasion during processing and use.
Lamination
Nanovia has a technology enabling the application of powdered adhesive granulate 80–200 µm or melt nets. Connecting the layers is done using pressure and temperature. A structure of lamination device allows to implement up to three layers in one step, or to divert the carrier layer which has the nanolayer applied on.
Lamination technology operating data:
- maximum operating width of 1800 mm;
- maximum processable winding diameter of 1200 mm at the input, xx mm at the output;
- tube diameter at the inlet of 76 mm, at the outlet of 76.
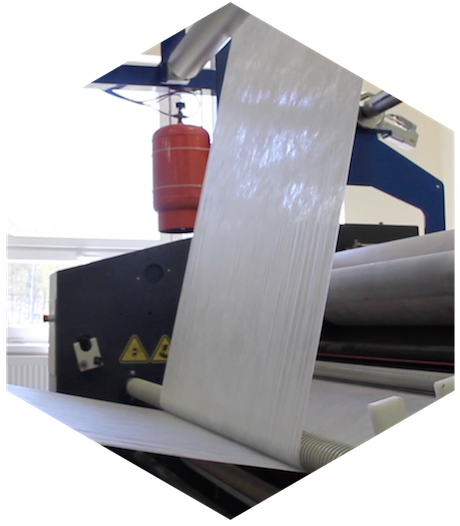
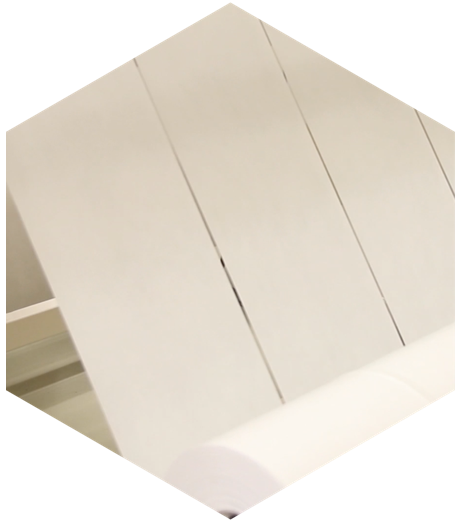
Cutting into the longitudinal stripes
After the material lamination, cutting the edges of laminate and adjusting the material to a final commercial packaging occurs. Nanovia also offers a full-width cutting of material into a narrow width, which is already intended for processing into the final product (mostly face masks and filters).
Forming technology operating data:
- maximum operating width of 1800 mm;
- maximum processable winding diameter of 1200 mm at the input, xx mm at the output;
- tube diameter at the inlet of 76 mm, at the outlet of 76;
- minimum strip width of 70 mm;
- maximum number of cutting discs 13;
- cutting accuracy +/- 1 mm.